Automatic diecutter 60T
- Pneumatic lock-up system on diecutting chase to increase efficiency
Easy slide in and out of diecutting plate is realized by air floating device
- Centerline system on diecutting chase with transversal micro adjustment ensures accurate registration thus results in quick job changeover.
- Aluminum gripper bar and positioning system, gripper plate 2-plate design
- All main drive chains are delivered in pairs from Japan and must undergo a special long-run test
- Equipped with reliable brake air clutch imported from Europe
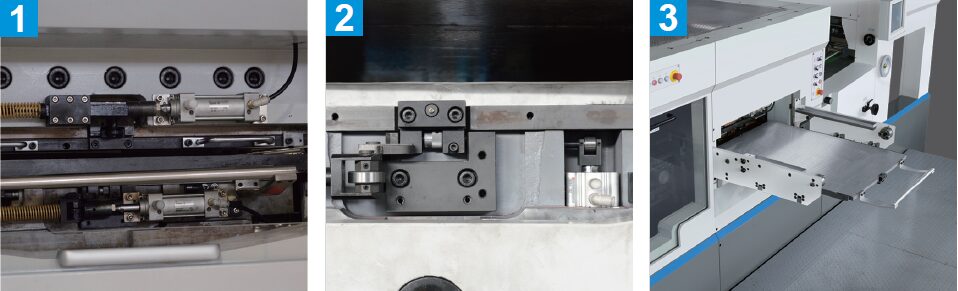
- Equipped with German design non-stop feeding system supplied by Mabeg Machinery (Shanghai) Co.,Ltd.
- Lateral blowing system is adopted to enhance paper separation. Equipped with electronic sensor to detect double sheet during transportation
- On the suction head, there is a micro adjustment device to adjust paper feeding to increase efficiency
- Standard machine is equipped with one side lay with sensor at the operation side
- Equipped with front lay sensor positioning system
- IVRS camera system for diecutting of digital printing product (optional) – with IVRS camera and servo driven side lay, machine can register paper position by printing mark on digital printing
- The installation of the anti-obstacle device on the feeding section is to prevent obstacle from entering into the machine which may cause damage on the machine
- 2 units of longitudinal foil feeding system as standard
- Foil rewinding unit and foil unwinding unit are inside the machine, changing foil and replacing waste foil can be done outside of the machine easily
- The whole unit can be slide outside of the machine and hence changing foil can be done easily
- Standard with 6 individually controlled heating zones with tolerance ±1℃
- Servo motors control pressure automatically with auto-drop pressure device
- Air blowing foil separation device is available
- Dwell time device is available for big area stamping
- Equipped with side alignment board to collect the pile tidily
- Safety photo-electric devices prevent over-ascending and over-descending of paper pile
- Adjustable depressor brush helps unloading paper from grippers and piling up paper
- Air-controlled rear alignment board switch design, easy to pick finished product sample
Maximum sheet size | 600×430mm |
Minimum sheet size | 297×210mm
Optional minimum sheet size:210×180mm |
Maximum stamping size | 584×420mm |
Paper thickness | 100-1200 g/㎡E flute corrugated paper |
Maximum pressure | 150 tons |
Maximum speed | 6500 sheets/hour |
Maximum stamping speed | 5000 sheets/hour |
Heating zones | 6 |
Number of foil rollers | 2 |
Maximum foil roll (diameter) | 120mm |
Max. pile height at feeder | 850mm |
Max. pile height at delivery | 850mm |
Main motor power | 7.5kw |
Total power | 15kw(Diecutting) 30kw(Stamping) |
Dimension | L2950×W1500×H1800mm |
Weight | 4.2 tons |
Categories